While doing some process development I'm also starting slowly with some design and realisation of parts of the next generation.
With the current piston it takes almost 2 days to produce a piston using the SLA 3d printer and this design also limits the maximum Z-height i can achieve.
For the next generation I want to explore a round piston instead of a square piston with rounded corners, this will allow the use of standard aluminium tube profiles and this will make scaling the Z-axis a lot easier.
The biggest advantage for the next generation is that i can use the current printer to make the more complex parts of the printer.
The printed part will be the connection between the inside of the piston wall and the linear guide system that moves the Z-axis up and down. It was printed with M5 threads in the design and after a quick finish with a tap the threads work perfectly, this is really nice because tapping threads in stainless steel can be very troublesome. It was printed in 9 hours and weighs roughly 140 grams.
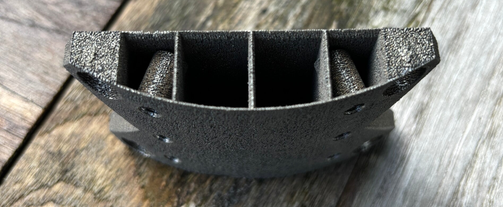
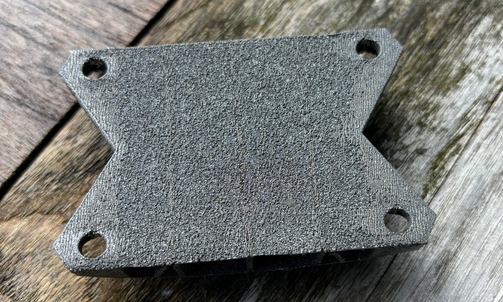
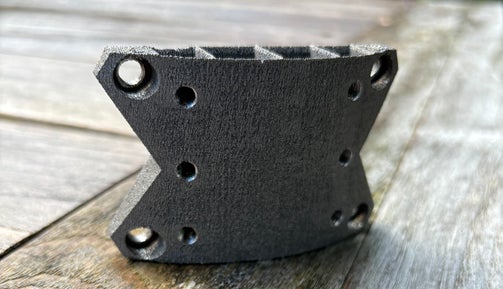
Add comment
Comments